Brewing Success
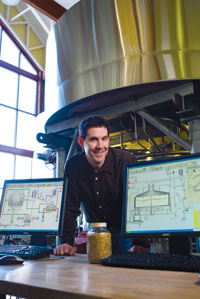
Lebesch was an electrical engineer by trade and member of a home brewing club. People began to talk about the quality of his homebrews and word of mouth led to a demand. The couple took the company commercial in 1991, and agreed that if they were going to "go for it" then they wanted the company to have a certain tone, according to Jay Richardson, director of IT for New Belgium Brewing. They established a set core values and beliefs for the company, with producing "world-class" beer being high on the list. Having fun is core as well, balanced by having "authentic relationships and communications."
Richardson explains, "This has led to other really prominent aspects of our culture like open book management. Except compensation data, practically every piece of financial information about the company is open to all coworkers." He says this goes hand in hand with the fact that all employees become owners through an employee stock ownership program after a year of service. "If you combine the implications of open book management with company ownership you can begin to understand how our culture is such a high involvement culture. There are certain rights that everyone enjoys and along with those rights comes a certain level of responsibility toward how we work, how we treat each other, how we treat our customers and how we treat our environment." Also important Richardson says, is "whimsy;" the idea of not getting too wrapped up in their work. "After all, we make beer," he points out.
Environmental sustainability is also at the heart of the company's values (see sidebar). "That's how we show up on our earth, how we treat it, and ideally, treat it in such a way that it's better off than before we existed," emphasizes Richardson. Doing this and being a role model in this area, he points out, doesn't have to be at the expense of the bottom line, contrary to what many may think. From the very beginning, as Lebesch invested in manufacturing technology, he did so not only with improved production processes in mind, but greater sustainability practices too.
Speaking of technology, Richardson says the use of information technology came along in the mid to late nineties. "The company started with buying a PC or two, along with Microsoft Office and then grew to having to share files over a small network and e-mail. We eased into IT in a way no different from a lot of small companies."
Technology Turning Point
Richardson cites 2003 as the turning point in the way New Belgium Brewing looked at new technology. It was increasingly difficult to make informed business decisions with the right data. For example, the company needed to be able to answer questions about growth and its effects. Senior management decided the organization needed to make better use of information that was available but hard to get. Along with this decision came the decision to hire an IT leader, Richardson was brought on board and he oversees the entire IT organization.
Also, the nature of an IT infrastructure is such that it grows as functionality demands increase. "Over time we started noticing - especially within IT - that an increasing amount of effort was required just to make things work together," he says. The more they started to talk to their co-workers the more they realized how many workarounds they had developed on their own. On top of that, IT realized there was a higher level of integration that could be achieved if there was a different back end. Primarily, it was an integration with e-mail where they were feeling the most limitations. "We wanted to spend less time making technology work and spend more time leveraging technology to help enable and support our company direction," Richardson concludes.
Thus, with the decision to make better use of information, the IT architecture would no longer be just networks and e-mail and PCs; it would be applications. The company owned Great Plains since 1997, and used it mainly for accounting purposes. Microsoft acquired Great Plains (now known as Microsoft Dynamics GP) and then changed the database structure to be that of Microsoft SQL server. Richardson says this opened the door to performing more analysis and applications-based activities.
"We put together an IT roadmap and that called for three main initiatives over three years: use Microsoft Dynamics GP as our ERP by implementing additional modules; implement a supply chain planning application; and implement a manufacturing execution system (MES) that will connect data from the automation systems on the plant floor to our back office systems," he explains.
While the ERP work began in 2004, New Belgium Brewing's use of the solution has been expanding ever since. Richardson says, "It has truly become the backbone for most of our business data." They started with implementing finished goods inventory and with that included some handheld computers and an increased level of automation at the warehouse. When trucks show up to load the beer, the product is checked onto the truck with the handheld, the bill of lading prints out automatically and all the associated accounting transactions are happening in the background at that moment. Earlier this month, they implemented a similar system for all of the company's raw materials used in the packaging process.
A supply chain planning application from Foresight Technologies was put in place a few years ago. It has a forecasting engine and analysis capabilities that are used by the supply chain team and salesforce. Planning and forecasting and having a lean supply chain are not the only concerns, however. At a recent strategic planning meeting, Richardson brings up, there was just as much talk of how the company can use its supply chain to reduce its footprint and make the environmental impact smaller as there was about how the company can reduce costs.
A Wonderware MES application with the ability to track and trace all the raw materials and movements on the production floor is up and running, effective last month. Richardson explains, "We were already using Wonderware as our human machine interface for all of our automation on the plant floor and that was another reason to go to a Microsoft infrastructure - Wonderware is tightly integrated with Microsoft."
The company's migration last summer involved moving to Active Directory, Microsoft Exchange Server 2007, Microsoft Office 2007 and Microsoft Office Live Communications Server 2005.
Richardson says the ratio of time IT spends keeping systems up and running versus enhancing the things that they have has definitely shifted. "We're becoming more of a project-based team rather than a firefighting team," he points out. "The benefits coworkers are going to notice are yet to come." For example, by the end of the month they will be rolling out Microsoft's unified communications system, and Richardson predicts it will "drastically" change how people communicate with one another especially with the remote salesforce.
And with the type of culture New Belgium Brewing has, sharing information and collaboration with coworkers is critical. Richardson explains, "As I mentioned in the beginning, there's an inherent level of responsibility that all our coworkers have. To ensure they're making the right decisions daily, people like to check in and bounce things off of one another. Communication and collaboration are extremely important to us."
After the unified communication system is rolled out, they will focus efforts on using the SharePoint tool set to make information readily available and easily navigable.
The company is also working with its distributors on getting consumer insight, and also purchases data from IRI to get some scan information. Richardson says that about a year and a half ago it partnered with a third-party data consolidator for the beer industry and subscribed to account level detail for New Belgium Brewing's products. "The data consolidator will grab sales information from the distributors' respective systems, roll it up, cleanse it and then send it to us electronically. We eventually load it up into a database and are able to analyze it here at the Mothership and wherever our sales coworkers happen to be," he explains.
Richardson mentions that having alignment and support with the business direction along with the support of senior leadership for IT initiatives is critical. Without it, no matter how good the technology is, it won't be adopted. He also advises other SMBs not to be intimidated by the size of Microsoft. "I have been really impressed with their latest roll out, the way things work out of the box and the kind of support we continue to get from Microsoft. For a 300-person company, the kind of support we are getting from a company the size Microsoft has been pretty impressive."