Burt's Bees Builds Energy-Minded Efficiency
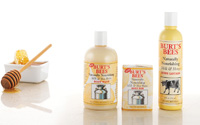
Burt's Bees has made its name through the tradition of corporate social responsibility. All of its products boast the highest levels of natural ingredients, nature-safe processes and environmentally sensitive packaging.
Challenges and Strategies
Burt's Bees is headquartered in Durham, N.C. Due to limited capacity at its main location, a portion of the manufacturing and distribution operations have been moved to multiple overflow facilities, including a third party logistics facility.
Still, Burt's Bees encountered some issues due to recent expansion in products and retail clientele, and the company was challenged to assess its current supply chain functions as well as develop a network solution. Determined to maximize operations while still protecting the environment, Burt's Bees turned to Tompkins Associates Inc., an operations-focused supply chain consulting firm, to install a new sensor-activated motorized drive roller (MDR) conveyer.
To avoid potential problems with storage capacity and customer shipments, Burt's Bees quickly sought Tompkins' help with the following criteria:
- Determine if Burt's Bees should outsource warehouse space; Due to costs, risks and timeline concerns of a third party logistics operation, it was recommended that Burt's Bees own and operate a new 144,000-square-foot distribution center (DC) in Morrisville, NC.
- Manage the implementation of the new DC; At startup Burt's Bees only needed 80,000 functioning square feet of the new 144,000-square-foot facility. However, with the new facility, the company optimized the capacity for future growth.
- Procure material handling equipment (MHE); Appropriate to the earth-friendly nature of the company, the MHE included the MDR conveyer that only runs when activated by sensors.
- Implement light version of the Tompkins Warehouse Control System (TCS); The solution is a full-featured commercial solution for warehouse and MHE control. The solution incorporates hardware redundancy and extensive internal event logging to provide faster problem resolution.
Sweet Success
Overall, the new solutions maximize the capacity of the DC, boost return on investment and minimize operating costs. In fact, energy usage is expected to decrease by as much as 40 percent to 60 percent. Furthermore, the new DC location improved operations and reduced warehousing and transportation costs. Burt's Bees can now consolidate finished goods in one building and meet growth projection without missing deliveries due to inventory issues.
Tony Quartararo, executive vice president supply chain for Burt's Bees, says, "The new facility and TCS have increased our efficiency, and we now have short-term and long-term solutions to help ease growing pains. Our customers can continue to expect a quality product delivered on time."