Inventory Optimization: Simon Ellis, Manufacturing Insights
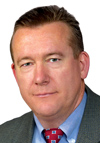
Inventory optimization (IO) technology has increasingly become an important tool to aid manufacturers in either managing overall supply chain inventories more efficiently or supporting decision-making processes with "what if" quantifications of the impact of certain business decisions on overall inventory investment.
This technology has moved beyond its previous "black-box" perceptions and has increasingly been adopted and deployed by leading-edge companies. Decision processes such as overall sales, inventory and operations planning, "profitable proximity" sourcing and new product innovation can all be aided by this technology.

Some software vendors persist in taking a "build it and they will come" approach to applications and technology, but not with IO.
The business challenges are quite clear. Typical business problems that an IO application can support include:
- How much inventory should I hold of each product, and where is the most cost-efficient point to store that inventory?
- Demand for my products is often seasonal or cyclical. How do I most efficiently plan and deploy overall inventory?
- How will a change in a supplier or production location impact my overall inventory cost or customer service levels?
The majority of IO offerings in the current market have been built around unique optimization algorithms, and each will yield a different result. It is therefore important for prospective buyers to do their homework in understanding the inventory or business planning problem needing to be addressed. Deployment of this application usually includes two types of approaches. In an interactive attended deployment, information inputs and outputs are depicted in the actual IO tool, and planners interact with the application to obtain inventory targets or perform analysis. In an automated deployment, the IO application sits in the background, with automated feeds of inventory or safety stock targets sent directly to the designated advanced planning system. In this mode, planners continue to interact with the planning system, but receive exception messages and certain analysis from some form of planning workbench that is fed by both the IO and planning applications.
A recent Manufacturing Insights survey of existing deployments among manufacturers indicates that the ROI for this technology can be significant and meaningful. Usability across vendor offerings is improving, helping in more rapid adoption. Deeper functionality, broader integration with supply chain network design, demand-aware supply management as well as planning workbenches have helped in adoption and user acceptance levels for the technology. Deployment can be accomplished in four to six months for initial managed scope deployments, facilitating inventory and other benefits for the business in less than a year.