Land O'Lakes Deploys a Catalyst for Change
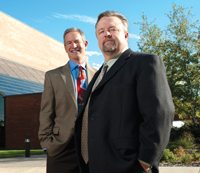
Dairy Foods -- Accounting for about $4 billion of total revenue, this business provides butter, cheese and powder products to customers in the retail, foodservice and industrial manufacturing sectors.
Land O'Lakes Purina Feed --The No. 1 livestock and lifestyle feed marketer in North America.
Winfield Solutions --The third largest farm seed business and No. 1 distributor of crop protection products in the United States.
This adds up to a $12-billion private agricultural cooperative headquartered in St. Paul, Minn. that does business in over 50 countries.
Historically, Land O' Lakes ran as a holding company with many separate entities. Over time, this resulted in an overly complex information technology (IT) environment, with no standardized instance of enterprise resource planning (ERP) or shared business practices. In 2005, a strategic decision was made to move toward an operating company model, centralizing certain core operations. The fragmented business processes and corresponding application architecture were simply not able to support this change.
That began to change when in 2005 Mark Thome, as vice president of Business Transformation and ERP, partnered with business leaders to simplify and standardize Land O'Lakes Financial and Dairy Foods application portfolio and business processes. This was a business initiative. In fact, Thome reported directly to two Dairy Foods general managers with a dotted line to IT.
"Business transformation projects are always challenging and in a manufacturing environment, the biggest impact is on the supply chain. To navigate the challenges and get value out of the investment, a strong relationship with the business is critical," says Thome, who is now vice president of IT for Dairy Foods and Supply Chain.
IT Alignment
Historically, Land O'Lakes used a handful of enterprise applications across its three business units. The company went as far as to designate JD Edwards (JDE), now owned by Oracle, as its go-forward ERP strategy in 2002 and acquired an enterprise license that was used to roll out its seed and feed businesses, but that's where efforts to standardize its entire IT environment stalled.
So much so that in 2006, Dairy Foods was still running on a combination of four ERP systems, none of which were JDE, leading to significant functional gaps.
"Because of the complexity inherent in a single business unit that contains separate retail, foodservice and industrial businesses, we knew migrating to a single unified ERP solution would be a major undertaking," says Thome.
A well-mapped out business transformation project, called Catalyst, was formed to migrate Dairy Foods from four ERP systems to just one, which encompassed the core transactions needed to plan, buy, make, sell, house, distribute and account for the business.
"The priorities for change were finance; moving to a standard, simplified chart of accounts; planning so we could reduce our days of supply and all related logistical costs; and transportation to optimize load utilization," reports Ken Litke, who at the time was vice president of Supply Chain for Dairy Foods. He is now vice president of Manufacturing. The company would also move to lot controlled inventory for quality and regulatory reasons.
With its priorities set, Land O'Lakes evaluated its technology options. Because JDE Enterprise One (E1) met key business requirements and was already installed at other divisions, Thome and his team chose to implement E1 with Oracle Transportation Management (OTM) for Dairy Foods
"Since we moved to an operating company structure during the project, it made sense to leverage what we had consistent with our fewer, bigger, better philosophy," says Thome. "We looked at other solutions, but the fit and the total costs of ownership were better with JDE and provided a more compelling business case."
The full scope of the implementation included applications for Financials, Production and Deployment Planning, Order Management, Shop Floor/Manufacturing, Procurement, Warehouse Management/RF Scanning, Transportation Management, Quality Management, Plant Maintenance (Asset Life Cycle Management) as well as EDI/XML (28 transaction sets/220 trading partners).
Deloitte Consulting served as the systems integrator for Catalyst.
"They have been a long time partner with Land O'Lakes and provided industry leadership as well as strong business transformation, project management and E1 knowledge and expertise. They were key contributors in our success," says Thome.
Smooth like Butter? To minimize business disruption to the degree possible and manage implementation risk, the company used a phased deployment over three and a half years that initially focused on cheese manufacturing. It also included corporate financial management. Phase two addressed the butter manufacturing, and phase three, the industrial process. The company tapped IBM's Websphere Enterprise Service Bus (ESB) to provide real-time integration between OTM and JDE.
"This was expensive and technically risky given the immaturity of the service oriented architecture capability at the time," admits Thome. "We determined the risk was worth it as we gained about half of our business benefits by integrating the two products."
They also leveraged standard integration technologies for production and deployment planning provided by JDE. Informatica was used to extract, transform and load (or replumb) the existing data warehouse to E1, necessary to enable the wave rollout approach.
As with any major change, Land O'Lakes made sure to understand and deal with its organizational readiness. In addition to training programs, human resources redefined the jobs that would be altered as a result of the new capabilities enabled by the transformation. And team dynamics were established by defining new governance and decision alignment structures and using the Land O'Lakes decision-making model.
As with most projects of this scope and size, Thome notes that the knowledge transfer is still a struggle today with continual changes in the business and in key user roles. "And we have opportunity ahead as we work to optimize Catalyst," he adds.
Challenges aside, the project was completed on time and on budget and it supports 2,770 users across the corporate campus, 12 plants, 40 third-party warehouses and 23 co-pack locations. Oracle was a strong partner in supporting Catalyst, in particular through a customer-focused program that JDE offers called Development Direct.
"This program gave us direct access to developers and the general manager of JDE," says Thome. "This was important strategically as we worked to grow the core code consistent with broader industry needs and tactically as we worked through complex technical issues that you inevitably encounter when doing projects like these."
A True Catalyst
At Land O'Lakes, Catalyst lived up to its name, delivering on its targeted internal rate of return and acting as a vehicle to eliminate obsolescence and close functional gaps.
For one, the company now has a more disciplined business process for lot managed inventory, both internally and externally, with electronic trace and recall capabilities.
Land O'Lakes simplified and standardized its chart of accounts from 6,000 to 1,300, and transitioned ownership to shared services to keep discipline around account control. It also achieved a no touch order compliance capability, which provides the ability to receive orders with no human intervention.
"The key is in order management," says Thome. "Today, that is the one application that touches everything and requires the kind of integration only provided by an integrated ERP system. It positions us to continue to progress on our perfect order journey."
These and additional new capabilities have led to significant quantitative results. The most notable include:
- Days of supply decreased five days
- On time delivery improved to 96.1 percent from 94.1 percent
- Case fill rate exceeding target at 99.3 percent
- Aged inventory reduced 66 percent from historical levels
- Truck weight improved 4 percent to an average of 40,000 pounds
For a breakdown of benefits by function, see the sidebar "Benefit Breakdown".
With the Dairy Foods ERP project behind them, Catalyst has been propelling a significant IT program to do the same thing for Land O'Lakes other business units.
"In addition, we are investing in S&OP integration, business intelligence and business analytics, especially in the agricultural side of our business," says Thome. "We are also investing in edge applications, like demand sensing and trade promotion management, which leverage our now stronger operational base."
Benefit Breakdown
Project Catalyst achieved its targeted return on investment in Land O'Lakes Dairy Foods Business. Here is a breakdown of the operational benefits gained as a percentage of the total:
Logistics: 48%
- Transportation costs down 4%
- Warehouse costs down 7%
- DC to DC finished goods movement reduced
Planning: 27%
- Obsolete and distressed inventory down 20%
- Butter conversion costs reduced
- Finished goods inventory reduced
General & Administrative: 19%
Sourcing: 5%
- Obsolete packaging down 50%
- Material costs reduced
Manufacturing: 1%
- Manufacturing effectiveness up 2%
- Reduced scrap by 5% (increased yield)