Richard Essigs of IBM on Supply Chain Visibility
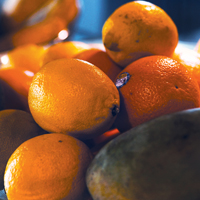
In a challenge to conventional thinking, let's ask ourselves: If some situations that we encounter in the marketplace are so new and unprecedented, is a different approach required to help ensure long-term success? Is it possible that in managing increasingly complex and rapidly changing supply chains, we too quickly jump to conclusions because we are looking for solutions to tomorrow's problems, using yesterday's answers? What if best practices are not the best approach?
The Evolution of The traditional Supply Chain
Consumer product manufacturers must address a number of unique marketplace dynamics in achieving the level of supply chain visibility associated with food safety and product traceability.
First, the pressure to drive down raw materials costs to maintain already thin profit margins has resulted in supply chains that source raw materials from lowest cost providers on a global basis.
Second, the increased role of both third party and global manufacturing in many supply chains has resulted in the need to monitor and maintain production standards in manufacturing environments outside immediate control. With increasing third party and global manufacturing, the potential for issues in adhering to approved processes and in complying with required standards becomes more prevalent.
Third, consumers now have unprecedented access to information regarding the contents and sourcing of products they use and consume, including food safety and product recalls.
Learning from mistakes
The next time senior management asks about best practices regarding food safety and product traceability, suggest a perspective that takes supply chain evolution into account; one that does not presuppose that best practices have already been discovered elsewhere. In addressing the challenges of food safety and product traceability, there is real value in learning from the mistakes others have made. Consider the following:
- Pride before preparation: Whether due to ignorance, apathy or denial, believing that it would not happen to their company is a mistake some have made. What can be learned from a company whose pride, which was built over 60-plus years, was erased by a lack of preparation in just six days?
- Consumers only know the brand on the package: Relying on third parties to maintain control over standards, without proper controls, is a mistake some have made. What can be learned from a company that didn't accept the reality that consumers hold the brands that they trust responsible for maintaining the highest level of standards throughout the supply chain?
- When optional becomes mandatory: Not recognizing and identifying the risks caused by a lack of repeatable processes and controls is a mistake some have made. What can be learned from a company that viewed supply chain visibility from the retail shelf backward as a forecasting and replenishment capability rather than as a necessity to meet today's food safety and product traceability requirements?
- Cost savings, but with a cost: In reacting to today's business pressures, there is a growing acceptance to implement solutions seeking to reduce supply chain costs, but isolate aspects of the overall supply chain. What can be learned from a company that focused on cost savings that forced them to pay the ultimate cost?
- If those already impacted by the challenges of food safety and product traceability could turn back the clock, would their fate have been different if they had answers to these five basic questions:
- Whether sourcing is done at a corporate, regional or local level, are consistent processes maintained across the whole enterprise?
- If raw goods suppliers are part of the supply chain, do all partners maintain adequate documentation to meet all regulatory requirements? Are these records maintained electronically?
- Is the visibility across multiple modes of transportation (ground, air, rail and ship) enabled by the transportation management solution?
- Who is responsible for the inspection and audit of company-owned and outsourced warehouse locations to ensure that consistent processes maintained across the enterprise?
- To what extent is ensuring visibility regarding delivery to retail stores automated? How well does this interface to other company applications to enable full supply chain visibility?
Consumer products manufacturers are making choices, often based on perceived best practices, to address a number of unique marketplace dynamics relating to supply chain visibility. Before presupposing that best practices have already been identified, remember that what seems to be today's best practices may not represent that best approach in the long-term.